The difference between valves acc. to ISO 15848 & bellow-sealed valves
Diminishing natural resources and expanding energy use are forcing the industry to regroup. The growing stringency of legal requirements obliges companies to use emission-reducing equipment (e.g. Net-Zero 2050 Initiative of the European Climate Foundation).
Leakage at different locations in the pipelines used in chemical plants produces emissions. Plant engineers can detect all these leakage points using different instruments and methods. The main leakage points include the valve/pump gland packing and flanged gasket joints. The modern chemical process industry is preparing itself to gain safer technology that contributes to better protection of the environment. The process engineer now has to design plants that curb the damage. They safeguard the environment, preventing the leakage of any poisonous chemicals.
Emissions are being monitored for almost all products available on the market today. Engineers need to comprehend the variances in the fugitive emission (FE) standards. These standards come from slightly different standpoints. Among the most common global FE standards in use today are the following:
- TA-Luft
- EPA 40 Parts 60/63
- End user specification from Shell Oil Company
- ISO 15848
Valves acc. to ISO 15848
Fugitive emissions from the valve to the open environment represent one type of leakage. The other type is leakage through the valve but contained within the piping system. Fugitive emissions are a potential safety hazard. They can also harm the environment. Leakage into the valve can be a safety hazard and can compromise the process.
The framework of ISO 15848 comprises “Industrial valves – Measurement, test and qualification procedures for fugitive emissions.” It subjects the whole industrial valve to type testing. These tests include body seals.
The ISO type test measures the entire industrial valve. It puts the valve into a temperature, pressure, tightness, and endurance class.
The ISO type test has precise and detailed requirements. As a result, it takes two weeks to do a complete ISO 15848 type test.
Info Box
"Industrial valves – Measurement, test and qualification procedures for fugitive emissions,” or ISO 15848, has two parts:
Part 1:
This part consists of qualification procedures and a classification system for type testing of industrial valves. The system distinguishes between three classes of tightness: A, B, and C. Class A has the least environmental leakage.
Part 2:
Production acceptance testing of industrial valves. It is an ISO requirement, but only for the products that have completed Part 1. It uses a helium leak detection test to check for leakage at room temperature without mechanical effects.
Characteristics of valves acc. to ISO 15848
- High wear resistant, hard coated stem thread.
- Non-rotating stem for low actuating forces and minimum wear of the sealing elements.
- Special thrust bearing of the stem/valve tip connection to absorb highest stem forces.
- Non-wetted parts in 316 stainless steel for operation in corrosive environments.
- Economic alternative to bellow-sealed valves.
- Colour coded dust cap for operating thread protection.
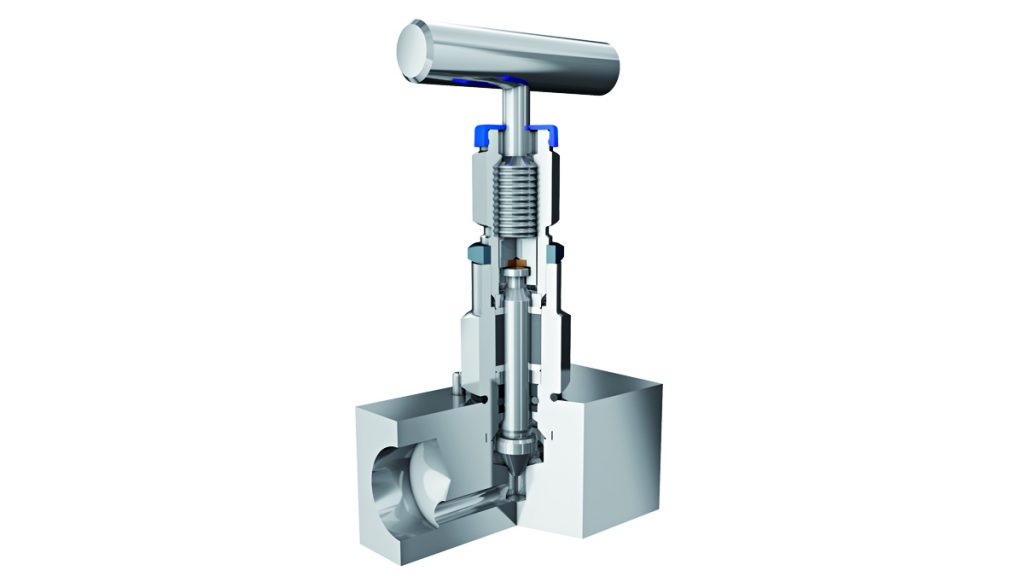
Bellow-sealed valves
The bellow-sealed valves are “technically leakproof.”
For some types of media, the material is so hazardous that even the minimum leak rate can be too high. In such cases, our Bellows Sealed Valves may be the best solution. To move the valve stem upwards and downwards without leaks, a multi-layer, metal bellow is used that is welded on the one side to the stem and on the other side to the valve bonnet. Therefore a leakage along the valve stem is not possible.
We weld a bellows seal inside the valve. This measure is the first sealing system. We use the safety packing as a second measure in the unlikely event the bellows gets broken.
Characteristics of bellow-sealed valves
- Robust sealing design with ‘zero leakage’ (no loss of fluids, better safety of the factory’s equipment)
- Long operating life with less maintenance (Fully flushed, multi-layer stainless steel bellows secured against rotating, designed for 2500 mechanical cycles)
- Bellows welded on one side to stem and on other side to valve bonnet
- Non-rotating valve tip in Stellite 6 material
- Safety packing
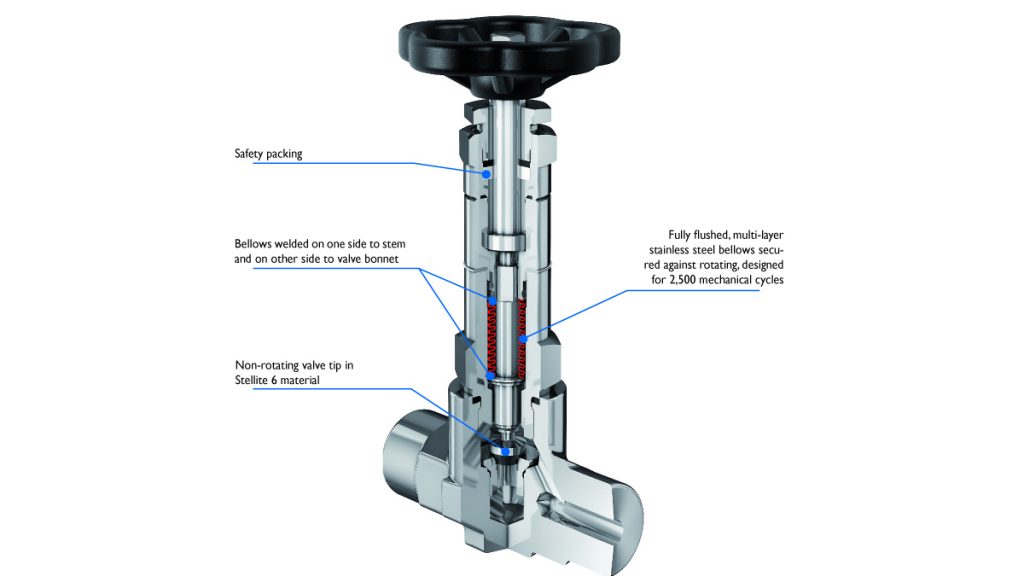
Info Box
Does a zero leakage exist?
Almost all valves leak by some measure from an engineering perspective. “Zero leakage” does not exist. Microscopic amounts of material may cross the seat or packing boundaries. The probability is higher if the gases used are “small molecule” such as hydrogen or helium. Class “A” of ISO 15848-1 allows “no visible leakage.”
(Image source: © Rawiwan / Adobe Stock & AS-Schneider)